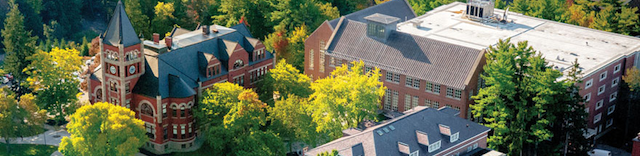
Honors Theses and Capstones
Date of Award
Spring 2013
Project Type
Senior Honors Thesis
College or School
CEPS
Department
Chemical Engineering
Program or Major
Chemical Engineering
Degree Name
Bachelor of Science
First Advisor
P. T. Vasudevan
Abstract
This project is a proposal to marry a coal gasification process to a biomass pyrolysis. Coal is pyrolized to produce syngas and a large amount of heat. The syngas is treated and fed to a Fischer-Tropsch process. The excess heat produces steam that is used to pyrolize biomass. The biomass produces char, gas, and vapor. The char and gas are recovered, and the vapor is condensed to produce bio-oil.
The proposed plant has a capacity of 1100 tons of biomass (550 dry tons) per day. I assumed an operating factor of 0.9 The plant could be operational within five years, with approximately three years of construction and a year operating at lowered capacity. However, significant research is needed to confirm and optimize certain aspects of the process.
The process has some sections at high temperatures and moderately high pressures. Certain units will be constructed of special materials to withstand the temperatures. Safety features will also be installed which will prevent temperatures from elevating beyond normal operating levels. A strong basic solution is also used to strip CO2 from process gases. These units will be constructed of stainless steel for structural integrity. Finally, highly combustible products are used in the process. Safe storage of these materials and strict fire safety provisions will be established to minimize the risks of fire or explosion. Safety considerations affected the capital cost of the plant because of the special materials required for safe construction.
The process does not have many environmental concerns. The gases produced by gasification and pyrolysis are collected as a byproduct to be used in a Fischer-Tropsch process. The disposal of liquid and solid waste is more of a concern. Solid slag can be disposed of in a landfill. Some liquid waste contains slag and ash and can be filtered. Other liquid waste has bio-oil contamination which is more expensive to remove. I made the assumption that this waste stream would need secondary treatment, which is fairly expensive and is a large contribution to the overall costs.
The total capital cost of the plant is around $30 million. For a chemical plant, this is not very large. The capital cost has a very minor effect on the production costs. To run the equipment, the plant will employ 45 process engineers, with 5 shifts of 9 operators.
Bio-oil can be produced for $1.77 per kilogram. Estimates for bio-oil produced from an unmarried process are hard to find, and have not been scaled to a current value. They range from $0.09 to $0.50 per kilogram. The large disparity between my price and the literature values is mostly due to the high cost of disposing water contaminated with bio-oil.
I recommend proceeding with research on ways to lower the operating costs. Specifically, if water contaminated with bio-oil can be disposed of with primary treatment rather than secondary treatment, the cost of production is lowered by $1.47 per kilogram, to $0.30 per kilogram. Lowering waste treatment costs will make the plant highly competitive with unmarried designs. Further research should also be conducted into other process parameters, such as the effectiveness of NaOH stripping, a novel technique I used to lower treatment costs.
Recommended Citation
Balch, Michael, "Married Coal Gasification and Biomass Pyrolysis" (2013). Honors Theses and Capstones. 108.
https://scholars.unh.edu/honors/108