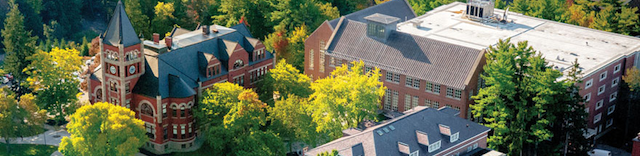
Honors Theses and Capstones
Comparison of Biomass to Bio-oils Reactor Systems: Direct Conversion vs. Companion Coal Gasification
Date of Award
Spring 2013
Project Type
Senior Honors Thesis
College or School
CEPS
Department
Chemical Engineering
Program or Major
Bioengineering
Degree Name
Bachelor of Science
First Advisor
Professor P.T. Vasudevan
Abstract
It is well known that the United States’ dependence on crude-oil negatively affects its economy, safety, and environment. To alleviate these negative consequences, a more economical and environmentally-friendly source of fuel, such as biomass, should be explored. The conversion of biomass to bio-oils involves the pyrolysis of biomass at about 500°C, thus requiring a great deal of heat. This heat source could be the excess waste heat from a coal gasifier.
As such, this report specifies the design of an industrial plant that produces bio-oils from biomass by using the waste heat from a coal gasifier. It is designed to produce 2.24×108 kg/yr of bio-oil that can be sold at $0.79/kg. This plant involves coal and biomass solids handling, a coal gasification reactor, a biomass pyrolysis reactor, and a series of separation units to remove waste products from the syngas and isolate the bio-oil. The syngas contains methane, hydrogen, and carbon monoxide and is sold as a by-product credit. The plant is expected to run on feeds of 1.5x1011 kg/yr of coal and 5.4 x108 kg/yr of raw biomass.
The coal gasification reactor was sized based on the heating duty of steam at 273000 kJ/s and the biomass pyrolysis reactor was sized based on a heating duty of 7026 kJ/s. The plant’s operating factor (POF) is 0.9 at 7884 hrs/yr running 24 hrs/day and 328.5 days/yr. The total bare module equipment cost, including all pumps, heat exchangers, grinders, separators, absorber, and reactors is $93 million. The total capital investment of the plant is $173 million. The DCFRR and NRR are 12.59% and 20% respectively.
Given that selling price of bio-oil ($0.79/kg) associated with this plant is about six times more expensive that the average cost of bio-oil ($0.13/kg), it is not recommended that a Class – 1 Estimate be conducted. Before a Class – 1 Estimate can be conducted, the unnecessary costs associated with this proposed plant must be addressed and reduced. Specific attention must be paid to the following two heat exchangers, E-127 and E-129. Additionally, attention should be given to discover a cheaper source of industrial, liquid oxygen.
Recommended Citation
Eicher, Alexandra, "Comparison of Biomass to Bio-oils Reactor Systems: Direct Conversion vs. Companion Coal Gasification" (2013). Honors Theses and Capstones. 106.
https://scholars.unh.edu/honors/106
Comments
The safety considerations include:
The key, innovative design features include: